Here’s an interesting blip in the data which search-watchers have observed: Google searches relating to “Industry 4.0,” especially “What is Industry 4.0?” have skyrocketed since the term was coined roughly a decade ago. However, actual real-world implementation has lagged well behind the clear interest that businesses have in the idea itself.
Industry 4.0 concepts promise a true new industrial revolution, one where smart computer monitoring and oversight of production facilities allow for significant new boosts in both product output and product reliability. Maintenance problems can be anticipated based on factors too minuscule for humans to notice directly, and ever-greater precision can be deployed throughout the manufacturing pipeline.
So why haven’t more businesses jumped onboard Industry 4.0, when it offers many clear advantages? We’ve heard a lot of reasons; these are some of the most common pain points that we get when discussing Industry 4.0 with our own clients.
“These systems will be too expensive to implement.”
There’s a perception that Industry 4.0 upgrades are prohibitively expensive. While it is true that some upgrades will be needed, the cost doesn’t have to be outrageous. Often, existing facilities can be utilized as they are, with the only cost coming from the addition of new digital sensors and monitors to the machinery that already exists. These can often be purchased off the shelf, and tied together in software.
We suspect this perception of expense is being largely driven by companies attempting to put together overly-ambitious bespoke solutions, rather than working with more commonplace hardware.
“Hardware will go obsolete too quickly.”
Another fear we often hear relates to the rapid pace of technological advancement. Basically, some companies are afraid of implementing a particular plan using particular hardware, only to discover that hardware has become outdated before it even comes online.
While this fear is rooted in truth, we feel that it shouldn’t be a factor in decision-making. Simply put, the pace of technological innovation has been accelerating steadily for the past century, and it shows no sign of slowing down. To wait for a single, stable, non-obsolete solution to come along would be to wait forever. Companies simply need to accept that they’re buying the best hardware as it exists today, while taking care to only partner with brands which will be able to offer long-term support.
And if something better comes out the next year, that’s just how things are with technology.
“There aren’t enough guides to implementation.”
This is, perhaps, the real crux of the matter. Industry 4.0 solutions are not “fire and forget” or “one size fits all.” Quite the opposite; they must always be designed specifically for the needs of each individual business. As a result, case studies are relatively rare, and case studies with any sort of global applicability are even rarer. Generally speaking, a company implementing Industry 4.0 upgrades must be willing to blaze its own trail.
This, of course, requires a certain level of fortitude and resolve among those executives choosing to investigate Industry 4.0. However, again, the key here is simply in doing research, focusing on sustainable upgrades which can be applied to existing workflows, and choosing partners who seem likely to remain stable in the years to come.
Industry 4.0 upgrades aren’t easy, but the benefits they bring will be more than worth it. Companies who take the plunge now will be well positioned to out-perform their competition for years to come.
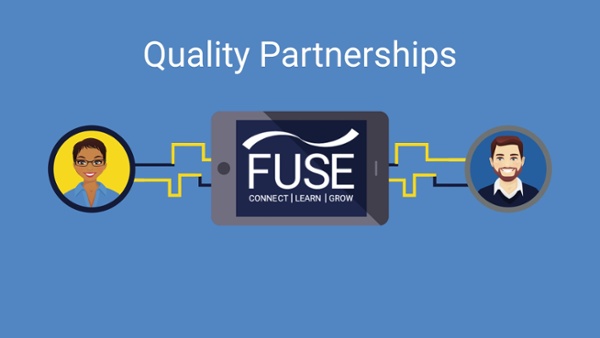