Right now, the American manufacturing industry is at a crossroads. Global manufacturing is still causing a lot of disruption, but American businesses have a significant technological advantage. It’s entirely possible for them to compete in a global market... but they can’t compete on price alone. They need to compete by offering better value. More features, more services, and products which are more reliable than overseas work.
This outlook creates the possibility for substantial growth and new sales – even to overseas clients. But there are unavoidable challenges in the way of seeing this happen.
Acquiring skilled workersFor decades, the American educational system has been focused almost entirely on the college pipeline, and that’s a big problem for manufacturers. Trade schools have been de-emphasized, and a great many young students who could have careers in industry are instead openly advised to look elsewhere. The result is a growing gap in positions vs people qualified to populate them, a gap which is only growing as Boomer workers rapidly retire.
Manufacturers should be proactive about this – in fact, they should be collaborating to fight these trends. Form interest groups. Do more promoting at high school job fairs and community colleges. Create digital ecosystems which tie trade schools more closely to the overall industrial ecosystem.
Manufacturers will need to help create more opportunities for better trade-focused education.
Implementing automation upgrades
Industry 4.0 technologies can revolutionize modern manufacturing. In particular, manufacturing processes overseen by “smart” AIs which can monitor hundreds of indicators at once can produce substantially better and more reliable products.
The problem, of course, is that such automation upgrades are expensive. Fortunately, costs are coming down, and automation specialists are becoming better at integrating upgrades into existing facilities with a minimum of new hardware investment.
However, these are upgrades which are absolutely needed to continue competing in the years ahead. Manufacturers should focus on looking at how these systems can reduce costs, and how these cost savings can largely mitigate up-front costs over the long term.
Embracing change
Industrial processes remained analog for a long time, longer than most fields – but American industry is finally hitting a point where it needs to embrace the digital transformation. Moving over to digital processes and data-driven decision making opens up numerous opportunities for cost savings, smarter business decisions, and an overall better ability to adjust to rapidly-changing market conditions.
The issue here is that the manufacturing industry is traditionally quite conservative, and there can be a lot of internal resistance to any sort of major changes to the workflow.
In many cases, new leadership is in order. Also, manufacturers looking to embrace modern digital techniques and Industry 4.0 practices should put as much emphasis as possible on the genuine benefits these transformations can bring to a company. The cost savings alone can easily justify the upgrades, not to mention the improved business intelligence angle!
Subscribe to FUSE today!
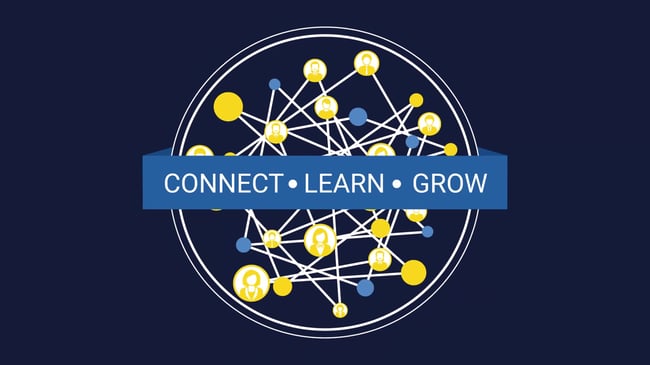